Common Polypropylene (PP) Compounds Used Across Various Industries
27 August 2024
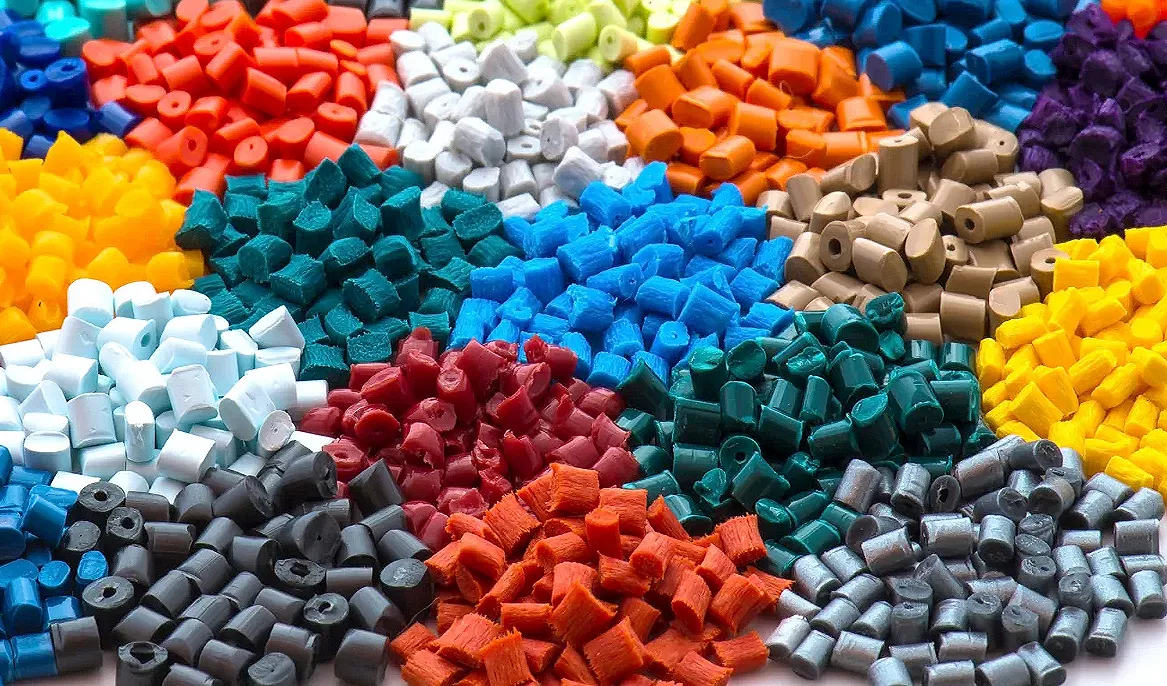
Introduction
Polypropylene compounds are widely recognized in the plastics industry due to their excellent processability, cost-effectiveness, high chemical resistance, low density, recyclability, and electrical insulation properties. These materials find extensive use in various sectors, including automotive, electrical and electronics, packaging, textiles, piping, household appliances, and more. Polypropylene compounds are created by mixing polypropylene resin (either homopolymer or copolymer) with various additives such as reinforcements, mineral fillers, impact modifiers, pigments, and others to achieve the desired properties. Depending on the final product requirements, manufacturers produce different grades of polypropylene compounds, which are explored in this article.
Common types of polypropylene compounds
1. Reinforced polypropylene compounds
Reinforcing polypropylene with glass fibers is an effective and economical method to enhance its mechanical properties. Adding glass fibers increases rigidity, thermal resistance, and toughness while reducing shrinkage. For example, heat deflection temperature (HDT) is increased up to 150°C (@ 1.8 MPa) for 40% glass fiber reinforced polypropylene.
Applications of glass fiber reinforced polypropylene are widespread, including in the automotive industry (e.g., front modules, rear and interior panels, mirror brackets, cooling fans, bumper brackets, engine compartments), household appliances (e.g., durable washing and dishwashing machine parts), construction, furniture, and electrical tools. In addition, due to low moisture absorption and lightness, these compounds are cost-effective and high-performance alternatives for polyamide compounds in many structural parts in different industries.
In addition to glass fibers, glass beads are also used to reinforce polypropylene, whose advantages include regular spherical shape, transparency, high compressive strength, high thermal stability, and isotropic shrinkage. Therefore, in cases where high compressive strength and reduced warpage along with improvement of surface quality are needed, this reinforcement is used instead of glass fibers. By using the combination of glass fibers and glass beads in polypropylene, at the same time, you can benefit from the advantage of the high stiffness of glass fibers and reduced warpage of glass beads.
2. Mineral filled polypropylene compounds
In these compounds, polypropylene is mixed with mineral fillers such as talc, calcium carbonate, and barium sulfate, available in micron or nanometer sizes, to improve properties and reduce costs. Among these fillers, talc is the most popular. The addition of fillers enhances stiffness, heat resistance, and dimensional stability while reducing creep. Different amounts of filler powder can lead to varying properties in the final product (table 1).
Table 1- Effect of different amounts of fillers on Polypropylene
Effect of Filles Example
Improved stiffness Adding 20% filler to polypropylene (homo) doubles the elastic modulus.
Nucleation effect Adding 500 ppm filler increases the crystallization temperature of polypropylene.
Reduced shrinkage Adding 20% of filler reduces mold shrinkage by 30-40%.
Enhanced dimensional stability Mineral fillers improve overall dimensional stability and reduce warping.
Decreased permeability 20% of filler loading in polypropylene increases by 50% moisture barrier.
Mineral-filled polypropylene compounds are widely used in automotive (e.g., dashboards, door panels, bumpers, grilles, HVAC systems), household appliances (e.g., dishwasher parts, air conditioner fan blades), packaging (e.g., rigid packaging), and piping and fittings industries.
3. Impact modified polypropylene compounds
Although polypropylene possesses desirable properties, its applications are limited by low impact resistance, especially at low temperatures. To improve impact resistance and reduce the risk of cracking or breaking, impact modifiers (rubber phases) are added during compounding. Common elastomers used include EPDM, SBS, and SEBS. These compounds are extensively used in the automotive industry for both interior and exterior trim components (e.g., door panels, rear shelves, dashboards, bumpers, fenders) and in packaging and consumer goods industries.
4. Conductive carbon black polypropylene Compounds
Incorporating small amounts of carbon black into polypropylene resin increases its electrical conductivity, fluidity, and impact resistance. Automotive manufacturers use these compounds to minimize static conditions in interior trim components. Additionally, conductive polypropylene compounds are used in electronic products, headphone cases, and electronic component pallets.
5. Flame retardant polypropylene compounds
In these Compounds, polypropylene is mixed with flame retardant additives to delay or prevent ignition. There are two types of flame retardant systems: halogenated (containing bromine, chlorine, phosphorus) and non-halogenated (mainly metal hydroxides like magnesium hydroxide and aluminum hydroxide). Non-halogenated flame retardants are generally less expensive but require higher dosages and can lead to greater loss of mechanical properties. Various standards and tests, such as Glow Wire and UL94, evaluate flammability. UL94 is the most commonly used standard, with results reported in V0, V1, and V2 levels, where V0 denotes the highest flame resistance and V2 denotes the lowest flame resistance. Flame-retardant polypropylene compounds are used in industries requiring high flame resistance, such as electrical and construction sectors, and also in some automotive components like battery covers.
Parsa Polymer Sharif’s Polypropylene Compounds
Parsa Polymer Sharif’s polypropylene compounds are based on homopolymer and copolymer polypropylene and are produced under the ParsaFill and ParsaFlex brands, as shown in Figure 1. To achieve sustainable development goals, some grades also contain industrial recycled content (PIR) and post-consumer recycled content (PCR) for specific applications.
Figure 1-Polypropylene compounds of Parsa Polymer Sharif.
These compounds offer ease of processing and can be directly used in various plastic processing methods such as injection molding, extrusion, and blow molding. Additionally, they provide a complete spectrum of mechanical properties suitable for different industries (Figure 2).
Figure 2- Mechanical properties of polypropylene compounds by Parsa Polymer Sharif.
ParsaFill
ParsaFill compounds are made from polypropylene combined with reinforcements and mineral fillers, available in heat stabilized, UV-stabilized, flame-retardant versions, and various colors. Reinforced polypropylene compounds, which contain short glass fibers or a combination of glass fibers and glass beads (10-50% by weight), offer high stiffness, thermal resistance, and impact strength. Mineral-filled compounds use fillers such as talc, calcium carbonate, and barium sulfate (10-40% by weight), providing high stiffness and good dimensional stability.
ParsaFlex
ParsaFlex compounds are high impact polypropylene compounds, available both with and without mineral fillers. They offer a good balance of stiffness and impact resistance and are used in automotive interior trim components like dashboards, door panels, and consoles. They are also available in scratch-resistant, heat stabilized, UV-stabilized, flame-retardant, and color-matched versions.
References
- https://europlas.com.vn/en-US/blog-1/what-is-compounding-in-polymer-common-types-of-polymer-compounding
- https://www.tasnee.com/en/products/petrochemicals/polypropylene-compound
- https://chemieuro.com/polymer-catalogue/polyolefines/polypropylene-compounds-pp-compounds