Introduction to the Polymer Compounding Process
08 July 2024
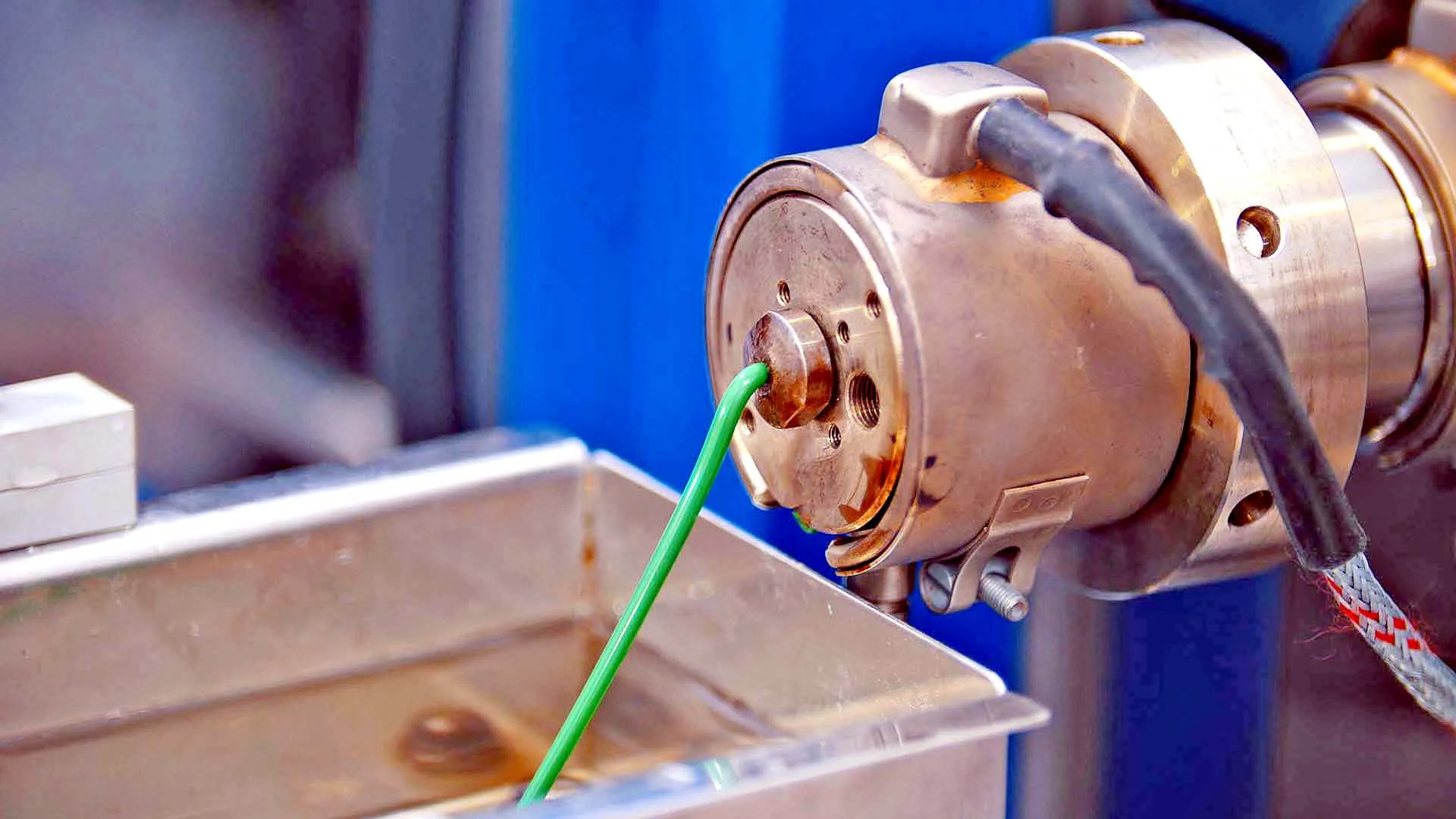
Introduction
Today, plastics have become an inseparable part of modern life due to their unique properties such as light weight, high durability, versatility, and low cost. They have found numerous applications. However, converting raw polymer resins into various plastics that meet the needs of different industries requires an important process known as compounding. Plastic compounding is a melt-mixing process in which polymer resin is combined with various additives to achieve specific properties. This process allows scientists and engineers to design materials that precisely meet specific performance requirements for various applications.
Stages of Compounding Production
Plastic compounding is a complex multi-stage process. As shown in Figure 1, these stages include material selection and formulation, pre-mixing, melting, cooling, pelletizing, packaging, and delivery to the customer.
1. Material Selection and Formulation
The first step in producing polymer compounds is selecting the base resin and additives and determining the formulation, considering the final properties and requirements of the compound. This stage requires extensive research and testing in the R&D department of each company. Common polymers used in the compounding process include polypropylene (PP), polyethylene (PE), polyamide (PA), polyethylene terephthalate (PET), polybutylene terephthalate (PBT), polycarbonate (PC), acrylonitrile butadiene styrene (ABS), polyvinyl chloride (PVC), and polystyrene (PS). The properties of the polymer resin can be affected by adding a wide range of additives, including antioxidants, reinforcements, fillers, UV stabilizers, impact modifiers, colorants, flame retardants, and more.
2. Pre-Mixing
The selected materials are carefully weighed according to the desired formulation and undergo processes such as drying, grinding, and pre-mixing to ensure uniform distribution and increase the efficiency of the additives.
3. Melting and Mixing
After physical mixing, the raw materials enter an extruder where they are heated, melted, and homogenized. Since temperature and mixing intensity are crucial in the polymer compounding process, twin-screw extruders are typically used. The screws create shear forces that melt the base resin under controlled temperature and pressure. Simultaneously, the molten polymer is thoroughly mixed with the additives, creating strong interfacial interactions, resulting in a homogeneous compound. Specific chemical agents can also be used to enhance compatibility between the additives and the polymer matrix, improving dispersion.
Sometimes, the molten compound may contain trapped air or moisture, causing voids and defects in the final product. To address this issue, the extruders used in compounding are equipped with degassing section to remove these volatile substances a combination of vacuum and pressure, ensuring the final product is void-free. After degassing, the molten compound is forced towards the die exit and finally extruded as thin strands through the die holes. The die is designed to filter the melt and create back pressure.
4. Cooling
The next stage involves cooling the strands by passing them through a water bath or air cooling system. During this passage, the temperature of the water or air is controlled to ensure proper cooling of the strands before they are pelletized, as the temperature affects the size of the produced pellets.
5. Pelletizing
After cooling, the strands enter a pelletizer, where they are cut into granules of precise and uniform size. Fine or oversized pellets are then separated using a sieve.
6. Quality Control
The granules are thoroughly inspected and subjected to rigorous tests based on the required characteristics. Parameters such as physical properties, melt flow index (MFI), heat deflection temperature (HDT), mechanical properties (tensile strength, impact resistance), electrical properties, color, and more are carefully evaluated to ensure the final compound meets the desired properties.
7. Packaging
Finally, the granules are packaged in large bags and placed on pallets for delivery to customers, where they can be used in other plastic processing methods such as extrusion or injection molding. Depending on the type of base resin, the produced compound may require an additional drying step to remove moisture before packaging.
Summary
Plastic compounding is a multi-stage process for converting raw polymer resins into advanced compounds with desired properties. Parsa Polymer Sharif, a leading company in polymer compounding, produces a wide range of plastic compounds using modern compounding systems and equipment (such as extruders and injection molding machines) and precise laboratory instruments, offering these products to various industries.
References:
1. https://www.bausano.com/en/technology/plastic-compounding-pelletizing
2. https://www.starplastics.com/plastic-compounding-101
3. https://www.palamaticprocess.com/blog/what-is-the-process-of-plastic-compounding-by-extrusion
4. https://www.rtpcompany.com/education/what-is-specialty-compounding