Common Challenges in Polymer Compounding: Strategies for Success
06 July 2024
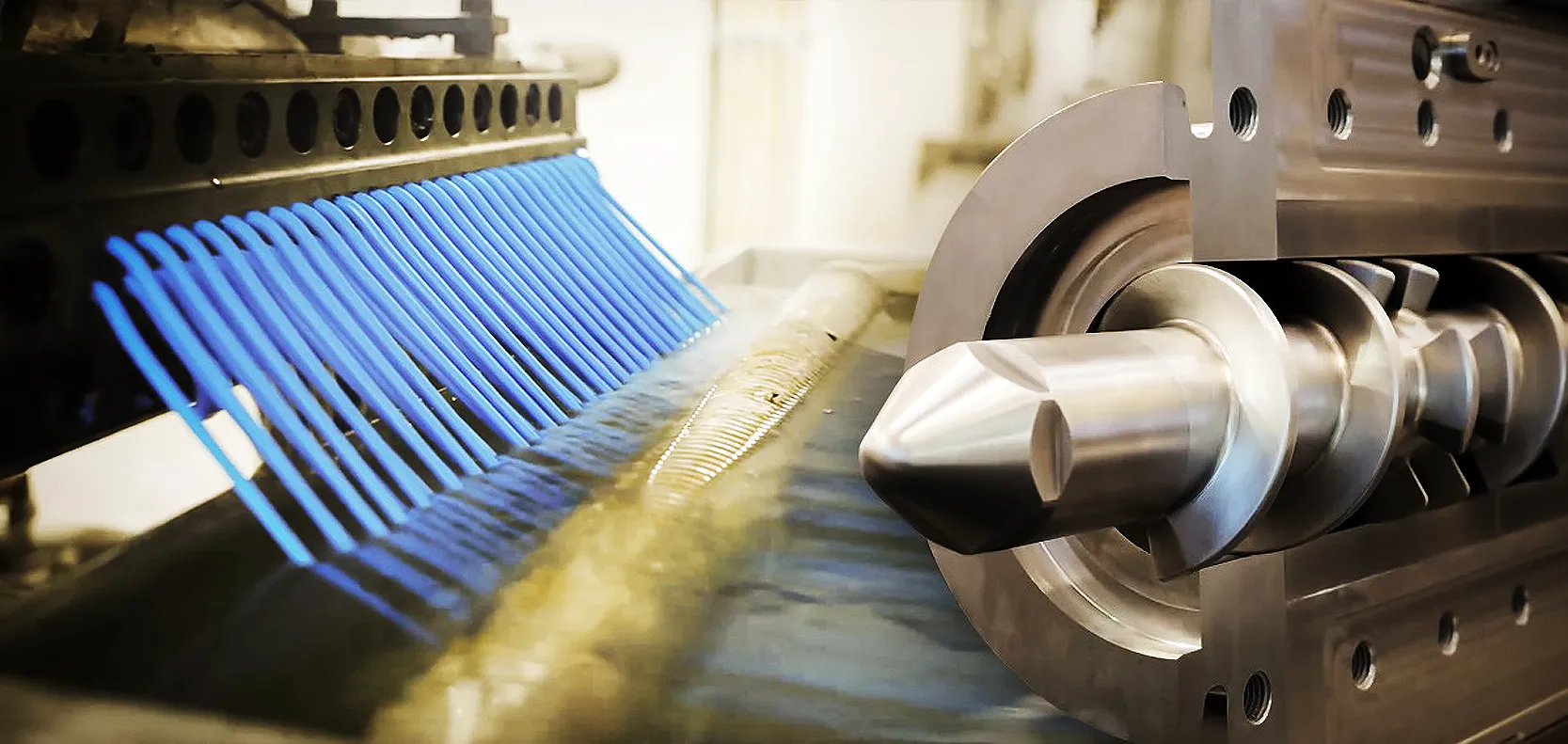
Introduction
Polymer compounding is a complex multi-stage process involving the blending of polymer resins with various additives to achieve specific properties in the final product. Typically, this process is carried out in a molten state with the aim of achieving a homogeneous blend. While compounding offers tremendous opportunities for product innovation and development, it also comes with multiple challenges that manufacturers must overcome to ensure quality, performance, and cost-effectiveness. This article briefly examines the complexities and common challenges in the polymer compounding industry along with strategies for effectively reducing these challenges.
1. Material Selection
The foundation of successful compounding lies in selecting suitable materials to meet the performance requirements of the final product. However, choosing from a myriad of polymer resins, fillers, reinforcements, and available additives in the market is a highly complex task. To overcome this challenge, manufacturers need to conduct comprehensive studies on material specifications, considering factors such as mechanical properties, chemical resistance, thermal stability, and their pricing. Collaborating with material suppliers and leveraging their expertise simplifies the material selection process, leading to improved compatibility among components.
2. Achieving Desired Properties
After material selection, the next challenge is achieving the desired properties in the compound formulation. Uniform dispersion of additives, particle size distribution, and compatibility among components are crucial factors affecting the performance of the final product. Utilizing advanced compounding techniques such as twin-screw extruders, reactive extruders, and masterbatch production enhances dispersion and uniformity of the blend, consequently improving its mechanical, thermal, and rheological properties. Additionally, conducting comprehensive tests such as melt flow index (MFI) measurements along with examining rheological and mechanical properties enables manufacturers to fine-tune formulations to meet desired performance criteria.
3. Process Stability
Maintaining process stability is essential to ensure consistent product quality and production efficiency. Changes in process parameters such as temperature, screw speed, residence time, and shear rate lead to fluctuations in the product properties and the increased defects. One solution for identifying and promptly addressing these variations is implementing robust process monitoring systems. Additionally, regular equipment maintenance, calibration, and operator training are essential tools for ensuring process stability and minimizing production downtime.
4. Cost Control
Cost optimization is an ongoing challenge faced by polymer compounders. Production costs encompass raw material expenses, energy consumption, waste generation, and labor costs. To reduce these expenses, manufacturers must adopt a comprehensive approach involving material efficiency improvement, process optimization, waste reduction, and capital management. Exploring recycling possibilities, using cost-effective alternative resources, and optimizing process parameters significantly impact overall costs while maintaining product quality and performance.
5. Regulatory Compliance
Making sure polymer makers follow strict safety, environmental, and quality rules is tough. The rules change depending on where you are and what you make, like keeping chemicals safe and controlling emissions. It's important to stay updated on the rules, talk to experts, and do things to follow the rules ahead of time. Using eco-friendly materials and processes, like recyclable stuff, not only helps follow the rules but also makes your brand look good and keeps you competitive.
Summery
Polymer compounding is a changing and growing industry. While it offers opportunities for creating new polymers, it also presents challenges such as material selection, achieving desired properties, maintaining process stability, controlling costs, and following regulations. To overcome these challenges, manufacturers need a strategic approach that allows them to deal with the complexities of the compounding process successfully.
Parsa Polymer Sharif, a forward-thinking company, addresses these challenges by utilizing cutting-edge technology and scientific expertise in their state-of-the-art laboratories. They specialize in producing high-quality polymer blends across six distinct product families to meet the diverse needs of various industries
References
1. https://www.conairgroup.com/resources/resource/top-5-challenges-in-plastics-processing/
2. https://resources.perkinelmer.com/lab solutions/resources/docs/WHT_PolymerLifecycleChallengesFinal.pdf