Additives in the polymer compounding industry
06 July 2024
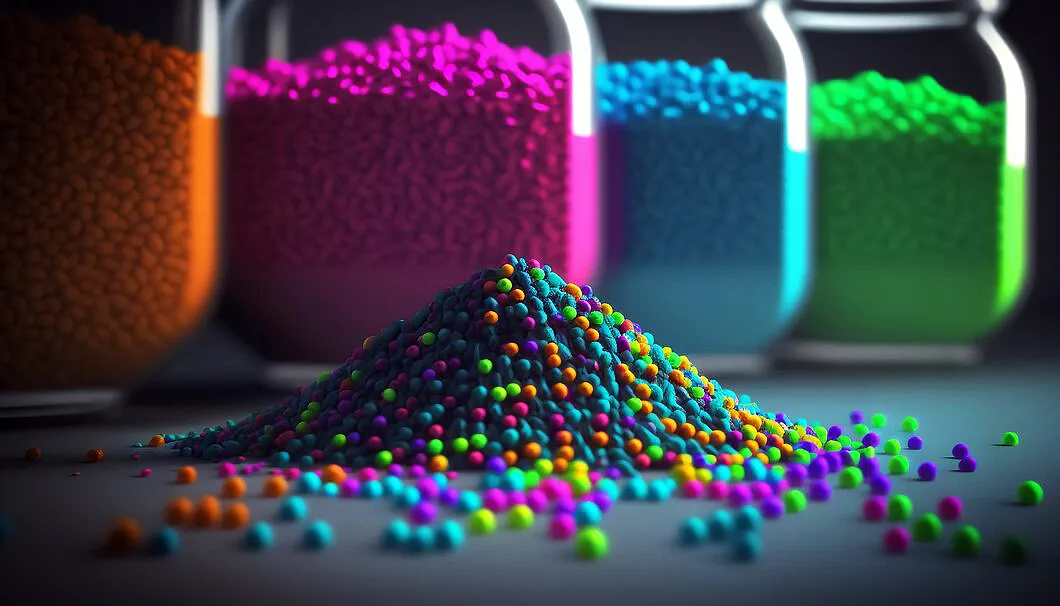
Introduction
In the polymer industry, additives play a crucial role in improving the properties and performance of polymers, enabling engineers to develop polymers for various applications in different industries. These additives can be in liquid, powder, or granular form and are usually added in small amounts (just a few percent) during the production process. This article aims to briefly explain the types of polymer additives, their functions, and their applications.
Introduction of key additives, their functions, and applications:
Antioxidants
· Function: Antioxidants act as protectors, combating processes that degrade polymers such as oxidation and thermal degradation, thus increasing the useful lifespan of plastic products. Polymer degradation occurs during both production and throughout their lifecycle due to environmental factors.
· Applications: These additives are used in plastic products containing resins with low resistance to oxidation, like polypropylene (PP) and polyethylene (PE), to prevent degradation during production, as well as in final parts such as pipes, fittings, and polymer films.
Fillers and Reinforcements
· Function: Fillers and reinforcements, including glass fibers, nanoparticles, and mineral fillers, improve the mechanical properties of polymers such as strength, stiffness, impact resistance, dimensional stability, and thermal stability, while also reducing costs.
· Applications: These additives are widely used in automotive, aerospace, and construction sectors, enhancing the durability and performance of structural components in these industries. Additionally, they find applications in sporting goods and appliance housings.
Plasticizers and Softeners
· Function: Plasticizers and softeners optimize the flexibility, elongation, and processability of polymers by altering their glass transition temperature (Tg) and increasing chain mobility.
· Applications: These additives are essential in formulating flexible PVC products like vinyl flooring, cables, and medical tubing. Furthermore, they improve the properties of elastomeric materials such as thermoplastic elastomers (TPEs) and thermoplastic polyurethanes (TPUs).
Flame Retardants
· Function: Flame retardants reduce the flammability of polymers and enhance their safety against fire. They interfere with the combustion process, suppressing flame spread or delaying ignition.
· Applications: These additives are primarily used in electronics and home appliances, increasing safety levels by preventing the spread of fire.
UV Stabilizers
· Function: UV stabilizers protect polymers from degradation caused by ultraviolet radiation, such as yellowing, embrittlement, and surface degradation, preserving the appearance and mechanical properties of products over time.
·Applications: These additives are predominantly used in outdoor components like automotive parts, agricultural films and furniture exposed to sunlight.
Antimicrobial Agents
· Function: Antimicrobial agents inhibit microbial growth in plastic products and prevent bacterial and fungal contamination.
· Applications: These additives are critical in healthcare settings, food packaging, and consumer products, ensure sanitary conditions and inhibit the spread of infectious diseases.
Conductive Fillers
· Function: Conductive fillers induce electrical conductivity in polymers, facilitating their use in electronic and electrical applications.
· Applications: These additives are vital in ESD materials, EMI shields, and electronic devices, enabling the development of polymer products with advanced electrical properties.
Compatibilizers and Processing Aids
· Function: Compatibilizers and processing aids improve the adhesion between phases, enhancing compatibility, improving phase dispersion, and reducing melt viscosity.
· Applications: Primarily used in blends, alloys, and polymer composites, these additives improve homogeneity, mechanical properties, and processing stability.
Impact modifiers:
· Function: Impact modifiers increase the energy absorption capacity of polymers by providing flexibility and toughness, allowing them to withstand impact without breaking. They can also improve the processability of materials by reducing the melt viscosity.
· Applications: Impact modifiers are suitable for applications where durability and impact resistance are critical and are used in a wide range of industries, including automotive, construction, consumer goods, and packaging.
Colorants
· Function: Color additives give polymers color, enhancing their attractiveness and beauty.
· Applications: Widely used in automotive, home appliances, packaging, consumer goods, and more.
Antifog Agent
· Function: Antifog additives modify the surface properties of polymers to prevent fog formation, ensuring transparency in polymer products.
· Applications: Common applications include food packaging (such as clear containers and films), agricultural films, automotive applications (like windshields, mirrors), and eyewear.
Antiblock
·Function: Antiblock additives reduce adhesion between polymer surfaces, preventing them from sticking during production, storage, or use, thus maintaining product quality.
· Applications: These additives are used in film and sheet production, reducing blocking problems, facilitating easy separation of layers in packaging, and improving overall performance of polymer films.
Lubricants
· Function: Lubricant additives increase the slipperiness or surface lubricity of polymer surfaces, reducing friction, improving processability, facilitating easy release of molded parts from molds, and creating smooth, non-sticky surfaces in final products.
· Applications: Common applications include film and sheet extrusion, injection molding, thermoforming, and packaging industries.
Scratch Resistance
· Function: Scratch resistance additives create a protective layer on polymer surfaces, reducing susceptibility to scratches and enhancing the appearance and lifespan of products.
· Applications: Typically used in products like electronic displays, automotive interior trim parts, and consumer goods.
Antistatic Agents
· Function: Antistatic additives reduce or eliminate static electricity buildup on polymer surfaces, preventing the accumulation of dust and dirt.
· Applications: Essential in the packaging of electronic components, textiles, and clean rooms to prevent static discharge damage or the attraction of contaminants.
Nucleating agents
· Function: nucleating agents facilitate the formation of smaller and more uniform crystal structures in the polymer matrix by creating nucleation sites. They also improve transparency and mechanical properties of the products.
· Applications: This additive is used in injection molding parts, films and packaging materials.
Antiodor
· Function: This additive neutralizes or hides unwanted odors caused by polymer products and creates a pleasant environment.
· Applications: This additive is usually used in parts such as car interior trims, shoes and home appliances to deal with unpleasant odors and improve the overall attractiveness of the products.
Optical Brighteners
· Function: Optical brighteners improve the whiteness and brightness of polymers, making their appearance more attractive under UV or natural light. They absorb invisible UV radiation and emit visible light in the blue spectrum range.
· Applications: Used in home appliance, textiles, films, and sheets to counteract yellowing or dullness caused by exposure to environmental factors, creating a clean and appealing appearance.
Summary
Engineers and material scientists have ample opportunities for innovation and product development in various industries by carefully selecting and combining additive materials in polymer formulations. Improvements in additive technologies are making polymer materials better for lots of different uses. Parsa Polymer Sharif Company produces a wide range of advanced polymer compounds through careful selection of additives and their appropriate concentrations. These compounds are produced in six families of ParsaFill, ParsaFlex, ParsaAmid, ParsaNova, ParsaAdd and ParsaBio, for use in various industries such as automotive, home appliances, electrical and electronic, lighting, pipes and fittings, packaging, railway and agricultural films.
References
1. https://www.degruyter.com/document/doi/10.1515/psr-2016-0130/html
2. https://amcorplastics.com/what-are-polymer-additives/
3. https://behinpolymerco.com/en/additives-revised/